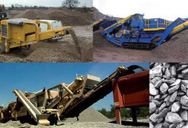
Comparative Study on Improving the Ball Mill Process
2021年2月19日 Optimization results confirmed that the balls to powder weight ratio were the most influential process parameter. The optimum process parameters setting
Онлайн консультация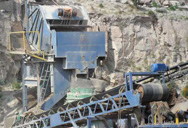
Enhancing the capacity of large-scale ball mill through
2020年5月1日 Abstract. The production capacity of the large-scale ball mill in the concentrator is a crucial factor affecting the subsequent separation and the economic
Онлайн консультация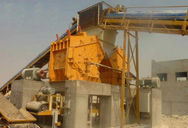
Improvement of methods to ensure energy efficiency of
The main factors affecting the efficiency of a ball mill are ball loading, drum rotation, lining wear. Optimal distribution of balls throughout the mill volume improves the efficiency of
Онлайн консультация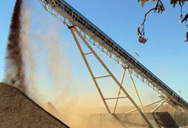
Effect of grinding media on the milling efficiency of a ball mill
2022年1月1日 Abstract. The size of grinding media is the primary factor that affects the overall milling efficiency of a ball mill (e.g. power consumption and particle size
Онлайн консультация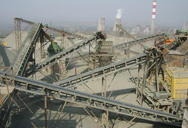
BALL MILLS Ball mill optimisation - holzinger
2021年3月12日 Ball mill optimisation As grinding accounts for a sizeable share in a cement plant’s power consumption, optimisation of grinding equipment such as ball mills can
Онлайн консультация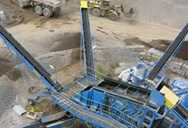
Impact energy of particles in ball mills based on DEM simulations
2022年1月1日 •. First-order grinding kinetics exists for ball mills. •. A correlation exists between specific impact energy and grinding rate constant. •. Grinding efficiency
Онлайн консультация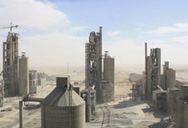
The energy efficiency of ball milling in comminution
2002年11月1日 Schellinger's calculated ball mill efficiency, in dry or wet ball mill grinding, ranges between 10% and 19%, with the higher figure occurring at the optimal mill
Онлайн консультация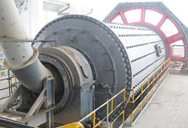
Energy Efficiency Analysis of Copper Ore Ball Mill
2021年3月23日 One method for increasing the energy efficiency of ball mills is to optimize their drive systems. This article looks at two variants of drive systems with efficiencies higher than the already existing solutions.
Онлайн консультация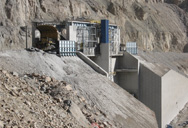
Analysis of process of grinding efficiency in ball and rod mills
2018年9月29日 The article presents the results of laboratory-scale research on the determination of the impact of ball mill parameters and the feed directed to grinding on its
Онлайн консультация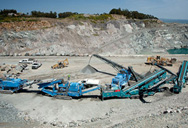
(PDF) Optimization and performance of grinding
2020年1月16日 The ball mill grinding efficiency was poor and could be indicated by the fraction 400 µm in the mill discharge. ... An improvement of product fineness up to ...
Онлайн консультация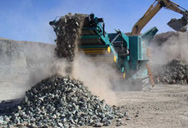
Improvement of methods to ensure energy efficiency of ball mills ...
2023年8月21日 The grinding process in ball mills is notoriously known to be highly inefficient: only 1 to 2% of the inputted electrical energy serves for creating new surfaces.
Онлайн консультация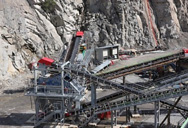
Improvement of methods to ensure energy efficiency of
2023年9月2日 The main factors affecting the efficiency of a ball mill are ball loading, drum rotation, lining wear. Optimal distribution of balls throughout the mill volume improves the efficiency of the grinding process and reduces energy costs. In addition, the properties of the ore are also impo rtant for the optimal operation of the ball mill.
Онлайн консультация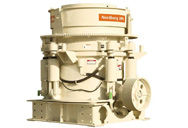
The energy efficiency of ball milling in comminution
2002年11月1日 In terms of this concept, the energy efficiency of the tumbling mill is as low as 1%, or less. For example, Lowrison (1974) reported that for a ball mill, the theoretical energy for size reduction (the free energy of the new surface produced during grinding) is 0.6% of the total energy supplied to the mill setup.
Онлайн консультация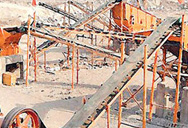
Energy and cement quality optimization of a cement grinding circuit
2018年7月1日 As can be understood, the circuit is closed circuited and is composed of a two-chamber ball mill, a mill filter, an elevator and a high efficiency air classifier. Within the circuit, the feed is ground in the ball mill initially. ... A critical analysis of energy efficiency improvement potentials in Taiwan's cement industry. Energy Pol., 96 ...
Онлайн консультация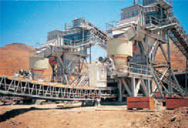
Improvement of the structure of a ball mill with the purpose
DOI: 10.15587/2706-5448.2022.260278 Corpus ID: 251552453; Improvement of the structure of a ball mill with the purpose of increasing the efficiency of material crushing @article{Kazak2022ImprovementOT, title={Improvement of the structure of a ball mill with the purpose of increasing the efficiency of material crushing}, author={Iryna Kazak and
Онлайн консультация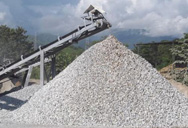
IMPROVEMENT IN RELIABILITY AND EFFICIENCY IN BALL
2019年9月23日 pulverization ball mill used in coal power plant There are total nine numbers BBD mills installed in three Units of Panipat Thermal Power Station. Each Unit is having three mills. Ball tube mills model BBD-4772 are installed in Unit-7 8 with coal crushing capacity as 75.9 Tons/Hour for design coal at ball load of 80 tons.
Онлайн консультация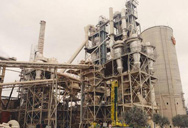
Study of the factors increasing the quality and productivity
2018年11月6日 The most used working regime of ball mills is described. The factors, affecting the milling process are examined. The factors, related to required energy for grinding: rotational speed of the drum, type of the mill shell and drum filling factor are shown. The factors used for increasing productivity and grinding efficiency are presented.
Онлайн консультация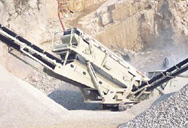
Analysis of process of grinding efficiency in ball and rod mills
2018年9月29日 The article presents the results of laboratory-scale research on the determination of the impact of ball mill parameters and the feed directed to grinding on its effectiveness and comparing it with the efficiency of grinding in a rod mill. The research was carried out for grinding copper ore processed in O/ZWR KGHM PM S.A.
Онлайн консультация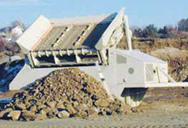
Improvement of methods to ensure energy efficiency of
Including metallurgical, enrichment and processing enterprises consume 5-20% of the electricity produced in the world. The main way to improve the performance of ball mills is to optimize the operating modes of the electric drive and mill equipment, to ensure stable operation of the ball mill and electric motor at full load.
Онлайн консультация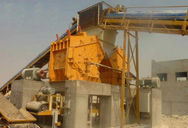
Study on the Performance of Ball Mill with Liner
2020年5月27日 2.3 Ball Mill Model The main structure of the ball mill is composed of three parts, namely the feed inlet, the cylinder part (work bin), and the discharge port. Figure 2(a) shows the structural model of a ball mill. In the mill cylinder part, there are lifters for turning over the particles. The quartz sand particles enter the cylinder through a
Онлайн консультация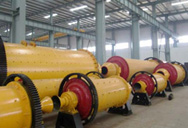
(PDF) Grinding in Ball Mills: Modeling and Process
2012年6月1日 efficiency of the ball mill and the economic assessment of the process control. R e f e r e n c e s . 1. A j a a l, T., R. W. S m i t h, W. T. Y e n. The Development and Characterization of a Ball ...
Онлайн консультация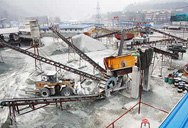
Modeling of Bauxite Ore Wet Milling for the Improvement of
2021年9月5日 Size reduction is a necessary operation in mineral processing plants and provides the desired size for separation operations and the liberation of the valuable minerals present in ores. Estimations on energy consumption indicate that milling consumes more than 50 % of the total energy used in mining operations. Despite the fact that ball
Онлайн консультация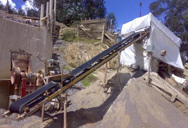
Improvement of the structure of a ball mill with the purpose
Downloadable! The object of research is the design of a ball mill for grinding dry materials, the subject of research is the efficiency of grinding material based on improving the design of a ball mill. One of the important problems for ball mills is the problem of reducing the efficiency of grinding material. The degree of grinding of materials in ball mills ensures
Онлайн консультация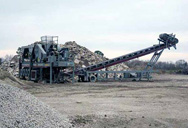
Improvement of the structure of a ball mill with the purpose
2022年6月30日 The object of research is the design of a ball mill for grinding dry materials, the subject of research is the efficiency of grinding material based on improving the design of a ball mill. One of the important problems for ball mills is the problem of reducing the efficiency of grinding material. The degree of grinding of materials in ball mills ensures
Онлайн консультация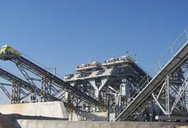
Ball Mill - an overview ScienceDirect Topics
8.3.2.2 Ball mills. The ball mill is a tumbling mill that uses steel balls as the grinding media. The length of the cylindrical shell is usually 1–1.5 times the shell diameter (Figure 8.11 ). The feed can be dry, with less than 3% moisture to minimize ball coating, or slurry containing 20–40% water by weight.
Онлайн консультация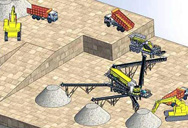
Determining the Bond Efficiency of industrial grinding
2020年9月24日 The metal Bond ball mill is 30.5 cm inside diameter and. 30.5 cm inside length, with rounded corners. It is smooth except for the door hole used for charging. The grinding charge consists of 285 iron or steel balls (43 @ 36.8 mm diameter, 67 @ 29.7 mm diameter, 10 @. 25.4 mm diameter, 71 @ 19.1 mm diameter, and 94 @.
Онлайн консультация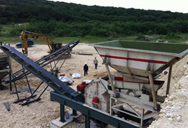
Addition of pebbles to a ball-mill to improve grinding efficiency
2016年9月1日 Abstract. Nkwanyana and Loveday (2017) used batch grinding experiments in a 0.6 m diameter mill to test partial replacement of steel balls (37.5 mm) for secondary grinding, by partly rounded ...
Онлайн консультация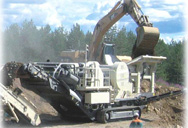
PROCESS ANALYSIS AND ENERGY EFFICIENCY
2016年11月23日 PROCESS ANALYSIS AND ENERGY EFFICIENCY IMPROVEMENT ON PORTLAND LIMESTONE CEMENT GRINDING CIRCUIT by Sixto Humberto Aguero B.S. (M echanical Engineering), Universidad Nacional Autonoma de Honduras, 1992 ... Low grinding kinetics at ball mill compartment 01, suggests improper size grinding media
Онлайн консультация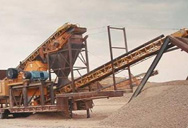
THE BENEFITS OF HIGH CLASSIFICATION EFFICIENCY IN CLOSED BALL MILL
2013年1月1日 increase ball mill circuit capacity by improving classific ation efficiency. It was estimated that circuit capacity may be increased by 15-25 per. cent by using fine screens to completely replace ...
Онлайн консультация